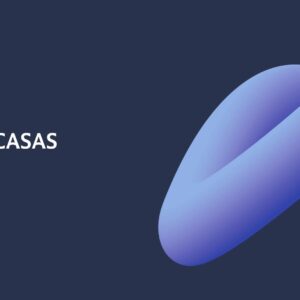
2 de abril de 2025
La industria no siempre falla por grandes errores. A menudo, lo que la debilita son pequeñas ineficiencias cotidianas que nadie cuestiona. Se repiten, se toleran, se normalizan. Y con el tiempo, terminan costando mucho dinero. A esto lo llamamos desperdicio invisible. Está en las planificaciones mal ajustadas, en los tiempos muertos, en los almacenes llenos sin sentido. Y afecta, sobre todo, a aquellas pymes que no tienen tiempo para parar y mirar.
Este reportaje se ha elaborado con la colaboración de José Alamar, CEO de Resultae, consultoría de negocio especializada en eficiencia industrial y estrategia operativa. Su experiencia con empresas industriales del área de Levante —especialmente en la Comunidad Valenciana y Murcia— aporta una mirada práctica sobre cómo detectar y reducir este tipo de ineficiencias.
Una fábrica puede funcionar, cumplir plazos y seguir generando ventas... y aun así perder dinero. ¿Cómo es posible? Porque lo que se escapa cada día en forma de tiempo, recursos y energía no suele medirse. Se trata de cosas sencillas a las que nos acostumbramos de manera sencilla y pasan a parecernos habituales como: Un cambio de formato que se alarga, una parada que se asume como inevitable, un stock acumulado "por precaución". No son errores graves, pero son constantes. Y por eso hacen daño.
El coste del desorden organizado
Las consecuencias del desperdicio invisible no siempre saltan a la vista, pero cuando se acumulan, acaban marcando la diferencia entre una empresa que crece y una que apenas sobrevive. Todo comienza con una sensación difusa: el margen ya no aguanta, los pedidos generan menos beneficio, y el ritmo de trabajo exige cada vez más energía para obtener los mismos resultados.
En el día a día, los equipos se ven obligados a trabajar con presión constante. Las áreas de producción y logística operan al límite, y los mandos intermedios dedican buena parte de su tiempo a resolver imprevistos. No hay espacio para anticiparse, porque todo se gestiona en modo reacción. Y cuando cada decisión se toma bajo presión, el margen de mejora se reduce.
Esta falta de estructura genera un tipo de fatiga organizativa que no aparece en los KPIs, pero que se nota en la moral del equipo y en la calidad de los entregables. Es el resultado de un "desorden organizado": un sistema que funciona por inercia, pero que está lejos de operar con eficiencia.
En muchas pequeñas y medianas industrias no se conocen con exactitud los costes por proceso, ni la capacidad real de cada línea. Se improvisa. Se trabaja con la urgencia como costumbre. Y aunque las intenciones sean buenas, sin datos concretos es imposible tomar decisiones que cambien el rumbo.
José Alamar, consultor industrial y CEO de Resultae, lo explica de forma directa: "El problema no es lo que se hace mal, sino lo que no se mira. Lo que nadie mide porque cree que no se puede cambiar. Nosotros ayudamos a ver eso que pasa desapercibido y que, sin embargo, está lastrando los resultados".
Lean no es una teoría japonesa ni una moda de grandes consultoras. Se trata simplemente de sentido común estructurado. Es preguntarse: ¿Esto que hacemos sirve para algo? ¿Aporta valor real al cliente? Si no, sobran pasos, sobran costes y sobra esfuerzo. Bajo esa premisa se definen cinco principios que ayudan a recuperar el control: identificar valor, mapear procesos, generar flujo, producir solo lo necesario y mejorar cada semana.
José Alamar añade: "Muchas veces, para romper las dinámicas creadas, es mejor que alguien externo observe los procesos. Así es más fácil identificar lo que los directivos y trabajadores no ven porque 'siempre se ha hecho así'. Desde fuera se detectan patrones que dentro se normalizan. Y ahí es donde suele esconderse el desperdicio invisible".
En la práctica, mejorar no siempre requiere grandes inversiones en tecnología. A menudo, se trata más de metodología que de maquinaria. Las herramientas Lean ayudan a organizar, visualizar y actuar, pero no son soluciones universales. Cada una tiene su momento y su utilidad. Saber elegir cuál aplicar depende del contexto y del problema a resolver.
5S: ideal para entornos donde el desorden es un problema habitual. Si el personal pierde tiempo buscando herramientas o materiales, esta herramienta es la primera que conviene implantar. Orden, limpieza y estándares básicos cambian el ritmo de trabajo sin necesidad de grandes cambios.
SMED: útil cuando los cambios de formato o preparación de máquina interrumpen la producción más de lo necesario. Con esta metodología, se pueden reducir drásticamente los tiempos de cambio sin afectar la calidad.
VSM (Value Stream Mapping): recomendable cuando no se tiene una visión clara del proceso completo. Este mapa ayuda a visualizar el flujo de valor de principio a fin, y detecta cuellos de botella o tiempos muertos.
Kanban: muy eficaz en empresas que sufren desajustes de inventario. Permite regular el flujo de materiales y evitar tanto roturas de stock como acumulaciones innecesarias.
Cuadro de mando operativo: necesario cuando se quiere hacer seguimiento de los indicadores clave del día a día. Permite a mandos intermedios y operarios tomar decisiones rápidas con datos reales.
TPM (Mantenimiento Productivo Total): ideal para instalaciones con alta dependencia de la maquinaria. Reduce averías, mejora el mantenimiento y estabiliza el ritmo de producción.
Estas herramientas no son recetas cerradas. Su eficacia depende de cómo se apliquen, quién las lidere y si hay voluntad real de mejorar. Pero todas parten de una premisa común: hacer más simple lo que hoy es complicado. Y eso, en una fábrica, marca la diferencia.
José Alamar lo ha visto una y otra vez. Lo cuenta sin adornos y con la claridad de quien ha trabajado desde dentro, “cuando el cambio se acompaña de método, se nota en semanas”. Y, como él insiste, no se trata de sectores concretos. Las metodologías Lean son aplicables a casi cualquier entorno industrial: desde la fabricación de componentes hasta la alimentación, pasando por calzado, químico o bebidas. Cambian los productos, sí, pero los cuellos de botella, los retrasos, las ineficiencias... tienen patrones que se repiten con distintos nombres y formas.
Recuerda, por ejemplo, aquella empresa de calzado que producía por inercia, con turnos que no encajaban y flujos mal definidos. No hizo falta más personal ni nueva maquinaria. Solo ajustar el ritmo, eliminar pasos innecesarios y dar visibilidad a lo que ya estaba ocurriendo. Resultado: un 40% más de producción.
O el caso de una empresa del sector metalúrgico, donde nadie había cuestionado los tiempos de preparación de la maquinaria. Se midieron. Se estandarizaron. Se entrenaron los equipos. Y la eficiencia creció un 21% en pocos meses. "Estaba todo ahí, pero nadie lo había mirado con lupa."
En la industria química, recuerda una planta que acumulaba paradas por problemas de coordinación y falta de mantenimiento. Rediseñar los procesos, introducir rutinas preventivas y ajustar responsabilidades generó un ahorro de 1,8 millones al año. "Y lo más importante: devolvió la confianza al equipo."
Y en el sector de bebidas, una reorganización de las operaciones y la logística permitió mejorar los indicadores clave: el BAI subió hasta el 6% y las ventas se dispararon un 20%.
Ninguna de estas historias empezó con una gran inversión. Todas empezaron con una decisión: dejar de asumir que "siempre se ha hecho así". Porque cuando el cambio se acompaña con método, los resultados llegan.
El desperdicio invisible no se ve en los informes, pero se nota en los resultados. Y en los ánimos. Verlo y actuar es la diferencia entre mantenerse y avanzar. Las empresas que ganan en competitividad no son las que trabajan más, sino las que trabajan mejor. El primer paso es siempre el mismo: medir. Porque lo que no se mide, no mejora. Y lo que no mejora, termina costando demasiado.